Installed in a 16th-century palazzo, Swedish fashion brand COS’s eighth consecutive Milan Design Week installation features a digitally designed and sculptural pathway of wood and bioplastic composite lattices comprised of 700 interlocking modular bio-bricks by London-based architect Arthur Mamou-Mani. Called Conifera, the pavilion’s unique construction suggests both legacy and ephemerality—its modular build allows the installation to be dismantled and reformed in alternate configurations in response to new contexts. Visitors can even observe one of the Delta WASP (World Advance Saving Project) Industrial 3D printers used to fabricate each of the bio-bricks in action. On a sunny day in Milan, as visitors wandered to and fro throughout the palazzo, we sat down with Mamou-Mani and Karin Gustafsson, COS’s creative director, to get the low-down on this year’s installation.
Arthur Mamou-Mani and Karin Gustafsson on COS’s Milan Design Week Pavilion
On a sunny day in Milan, as visitors wandered to and fro throughout Palazzo Isimbardi, we chat with Arthur Mamou-Mani and COS creative director Karin Gustafsson to get the low-down on Conifera, this year’s Milan Design Week installation.
BY RYAN WADDOUPS April 12, 2019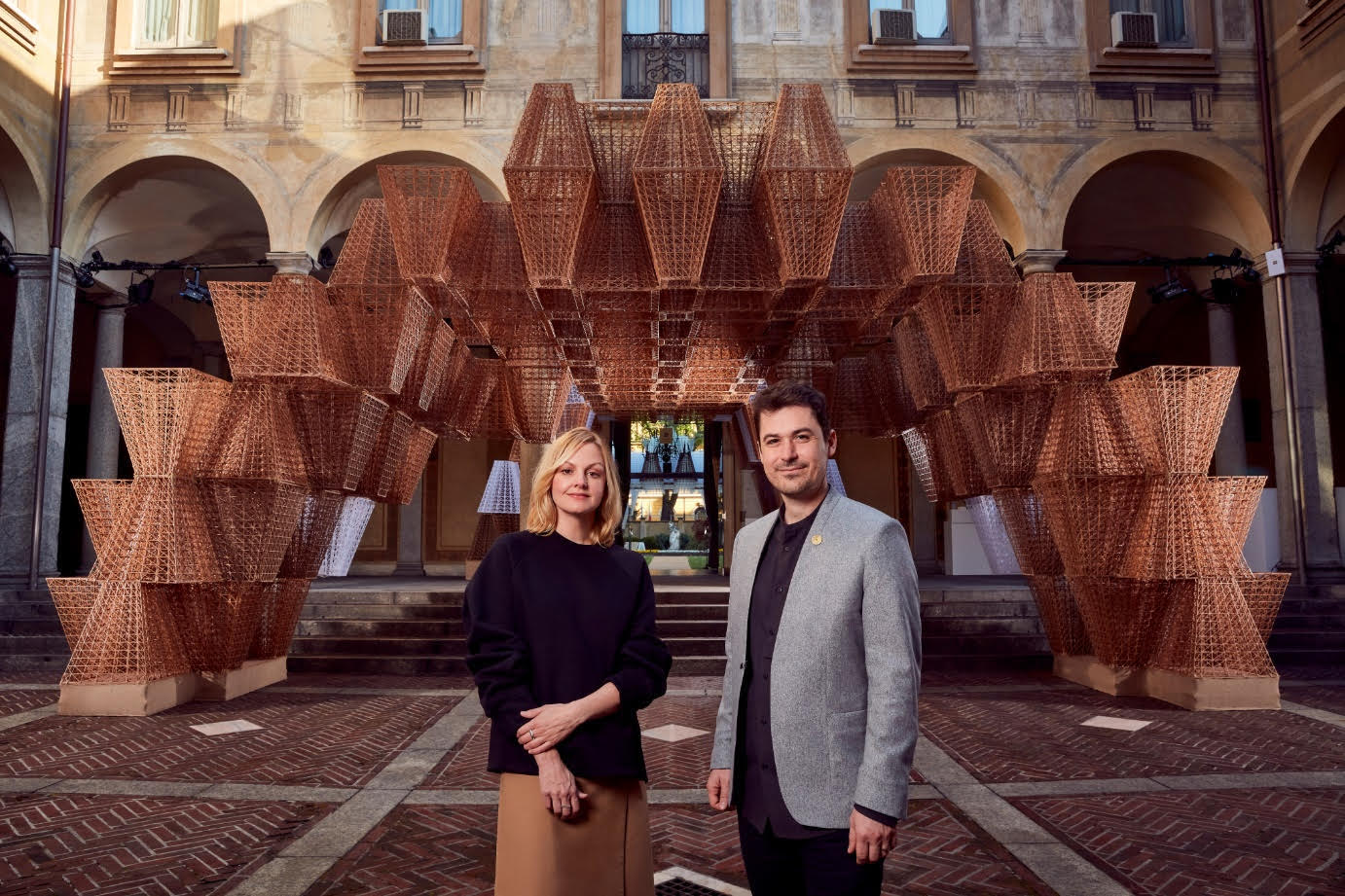
First thing’s first—after such a grand reveal, how are you? How has this year’s Salone been going?
Arthur Mamou-Mani: I’m both excited and tired! It’s a strange feeling—is there a word for it? Conifera was a huge challenge. We pushed everything possible in terms of material innovation and 3D printing capabilities. We had the right technology in the right moment. It ended up being such a beautiful, collaborative process engaging, discussing, iterating with COS and all these 3D printing labs around Europe. A fulfilling process but obviously very intense. I’m glad to still be standing!
Karin Gustafsson: Unveiling Conifera was such an exciting moment. It was on the drawing board for so long, but experiencing it in real life is so different—it really makes you feel something. And people are enjoying it! We had more than 4,800 visitors on opening day.
Tell me about how the collaboration started. Karin, how did you first learn about Arthur’s work?
KG: We thought Galaxia, his 65-foot-tall timber sculpture at this past Burning Man, looked amazing. I started researching Arthur’s work and really identified with his approach, so we started a conversation.
AMM: Galaxia was extremely meaningful, so we thought Conifera could be a continuation of sorts. We talked very openly with COS and learned that we share the same values regarding the plastic waste crisis, sustainability, and democratizing creativity. Our conversation got me excited to use our open-source tools and design something beautiful in an inexpensive material that integrates all the values I’m passionate about.
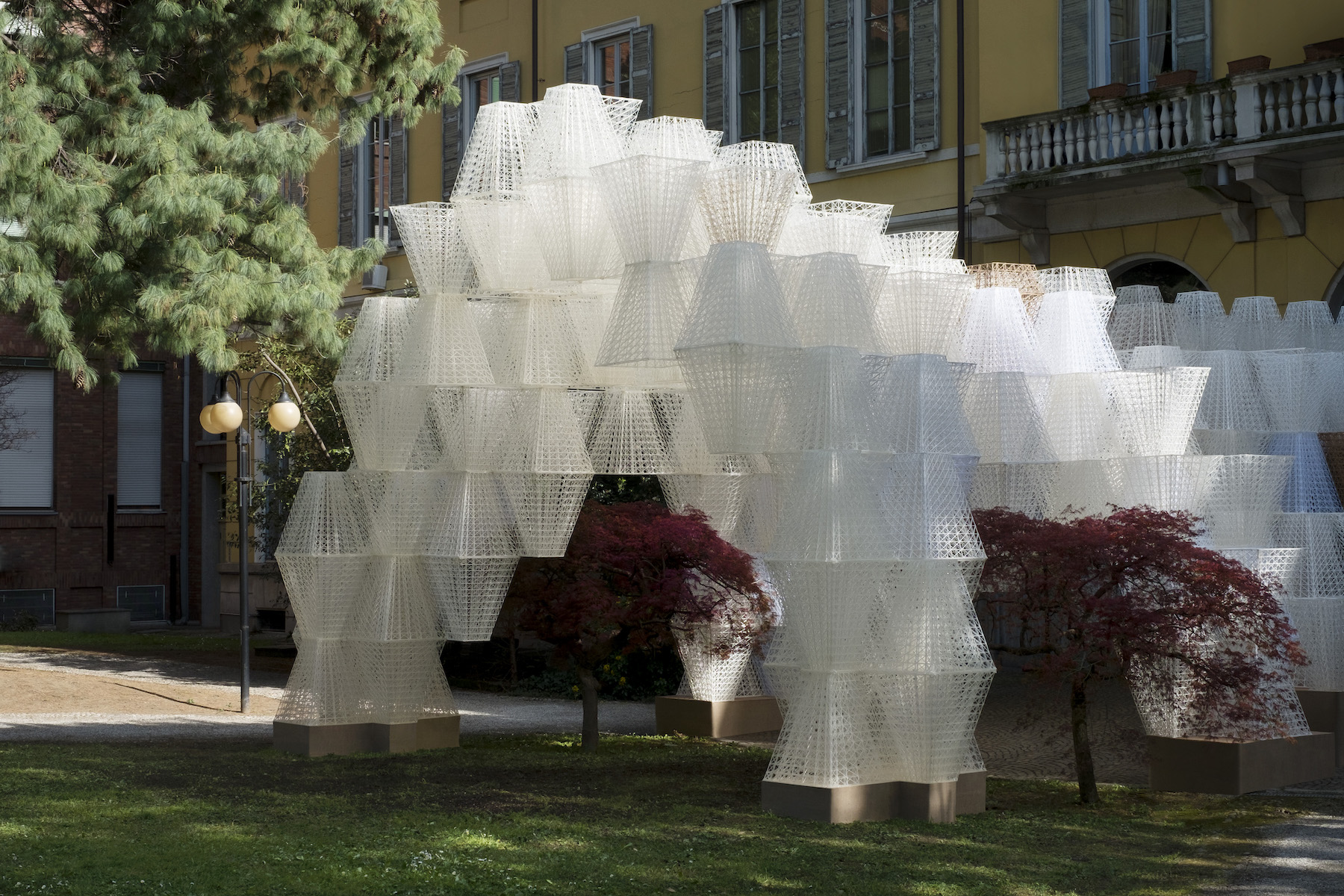
When the collaboration was agreed upon, Arthur, what was your first plan of action?
AMM: Architects always see geometry first. There was an interesting contrast between the courtyard’s rectilinearity versus the organic, free-flowing nature of the garden—almost a yin-and-yang relationship. I thought Conifera could reflect both, and transcend the manmade and natural, the monumentality and lightness.
What technological challenges did you encounter along the way?
AMM: Palazzo Isimbardi is large, so Conifera needed to have a strong visual impact. You must optimize the 3D printing process to create something that substantial. Our approach involves designing the printer’s movement directly in the computer. Imagine someone holding a pen, trying to not lift their hand while finding the most optimal pathway through a zigzagging lattice. That’s the mathematical challenge: to maximize speed, minimize the amount of material, and discover an assembly process that makes sense. We iterated, started production, continued to iterate, arrived on site, continued to iterate, and so on.
One major concern about 3D printing is the use of plastics, but this pavilion uses organic materials.
AMM: Polylactic acid (PLA) is a very common biodegradable material invented by an agricultural company specializing in corn. Essentially, it’s a thermoplastic derived from renewable biomass, typically from fermented plant starch such as from corn. We extracted long chains of polymers from corn to create these bioplastics, which are much more efficient than oil-based plastics.
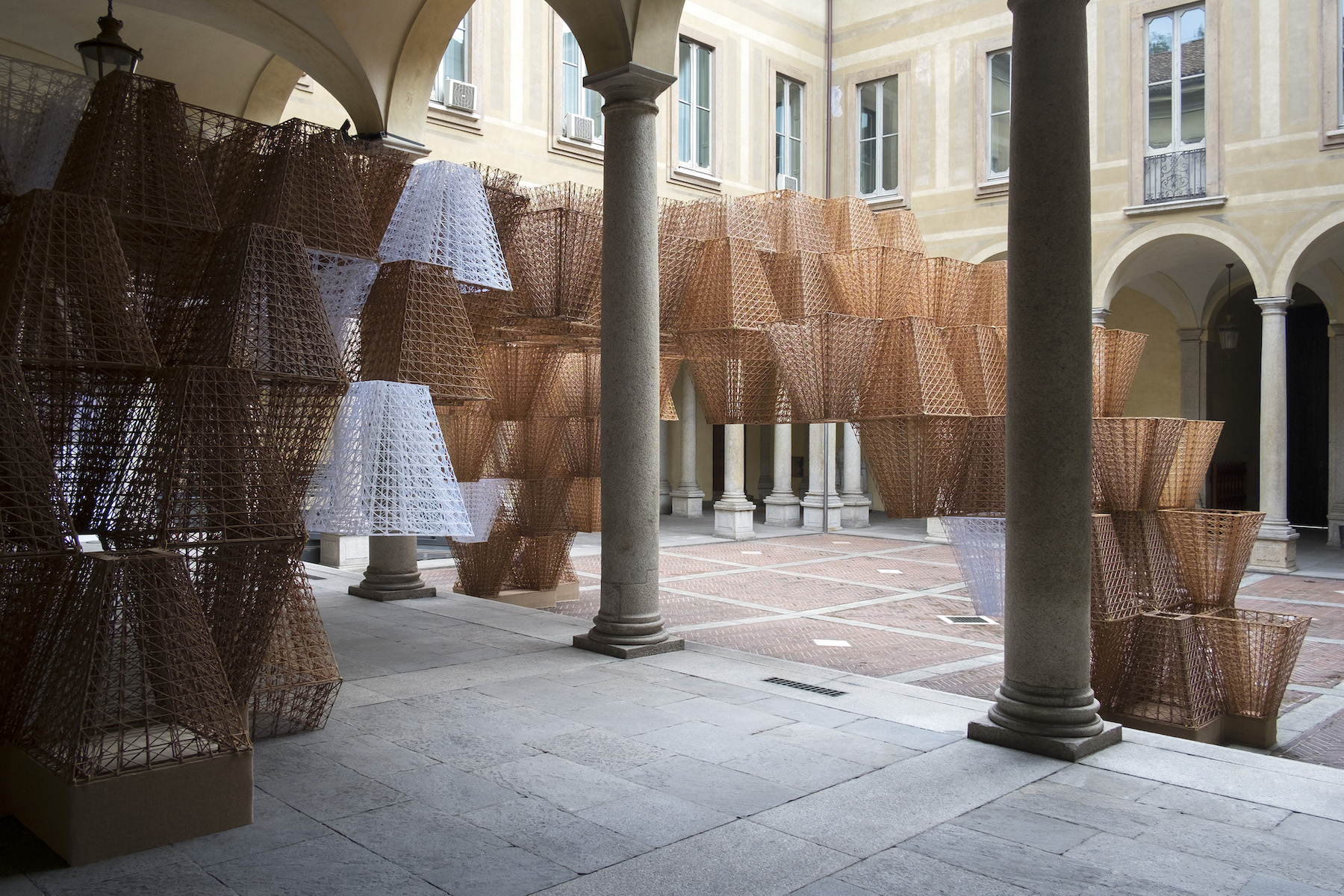
What has this project taught both of you about the power of materials?
AMM: Materials are the starting point of design. Many of our projects start from simply choosing materials. The idea of maximizing an inexpensive material through a technique-led approach has so much potential. It’s both accessible and teachable, which are very important to me—I’m a teacher, after all.
KG: Materials impart emotions that wouldn’t otherwise resonate through a screen or on paper. The 3D printed elements really make Conifera come alive—there’s a certain richness to it.
The pavilion also harnesses some curious features of wood.
AMM: Some of Conifera’s components mix PLA with wood pulp to create caramel-color bricks. The wood’s cellulose mixes with the polymer chains to create a wood-plastic composite, commonly used for outdoor decking. It’s a huge industry that still uses oil-based plastics which is unfortunate because bioplastics produce 68% less carbon and are nontoxic.
Designing within the parameters of a historic 16th-century Palazzo is no easy task. How did the site and architecture inform the end result?
AMM: Palazzo Isimbardi’s monumentality completely contrasts the temporary city of Burning Man! So much of Conifera draws from the palazzo. It’s important to be cognizant of a project’s surroundings instead of simply imposing something new. For example, the courtyard’s geometry became fractalized throughout the project. Each brick’s cross-section is a series of overlapping squares, and the courtyard’s herringbone pattern appears in the motif. We referenced Italian culture, too—the truncated pyramids, when stacked atop one another, pay homage to Constantin Brancusi’s Endless Column.
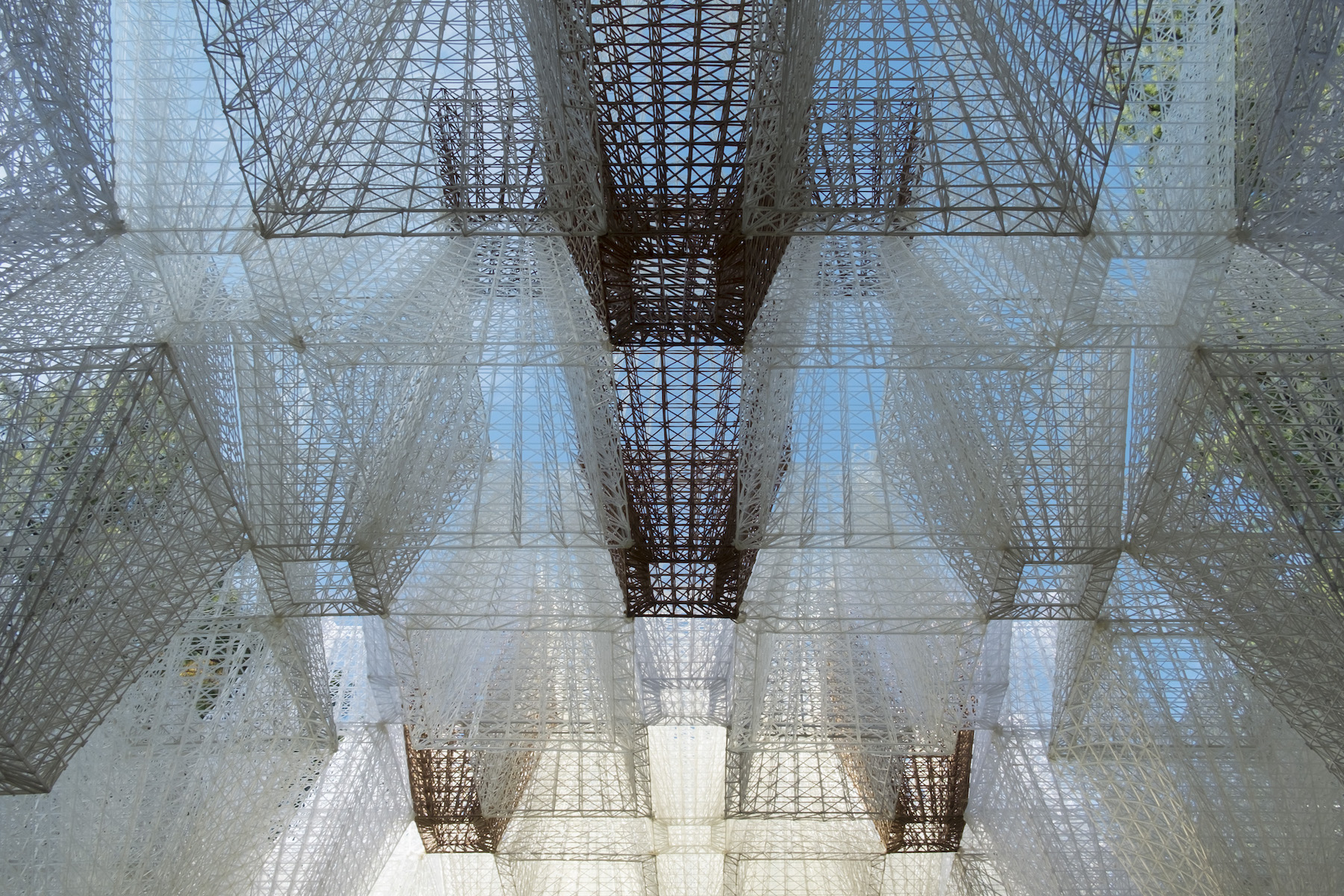
What are some of the most useful applications of bioplastics?
KG: It’s a hard material, so it’s something COS might explore for jewelry or prototyping.
AMM: We can infrastructure roofs, partitions, flooring, and furniture. It opens up a whole new world for us.
Has COS incorporated 3D printing technology? How do you think it can upend the fashion industry?
KG: We’ve explored it for prototyping worn objects and jewelry. We’ll have to wait and see—every new technique is interesting. For example, we’ve started to explore seamless knitting, which simplifies the production process and makes garments more comfortable.
How are both of you designing to address the environmental needs of tomorrow?
AMM: I believe in the localization of production. To produce Conifera, my office in London emailed the code to 3D printing facilities around Milan. It became an exercise in minimizing shipping while considering the full material life cycle, which ends at the composting facility in Milan. Ultimately, the material ends up back in the earth, so the cycle starts again. Recognizing the potential of this cycle takes an open mind, so I’m happy that COS and I were on the same page. They even did the research to find the composting facility and respected my concepts from start to finish. We definitely helped push each other.
KG: We prioritize making high-quality products from the beginning, which takes a certain faith in craft and innovation. We always reference old production techniques while exploring potentially better solutions for the future. We aim to offer long-lasting products that bring extra value to the table so you keep them, not throw them away.
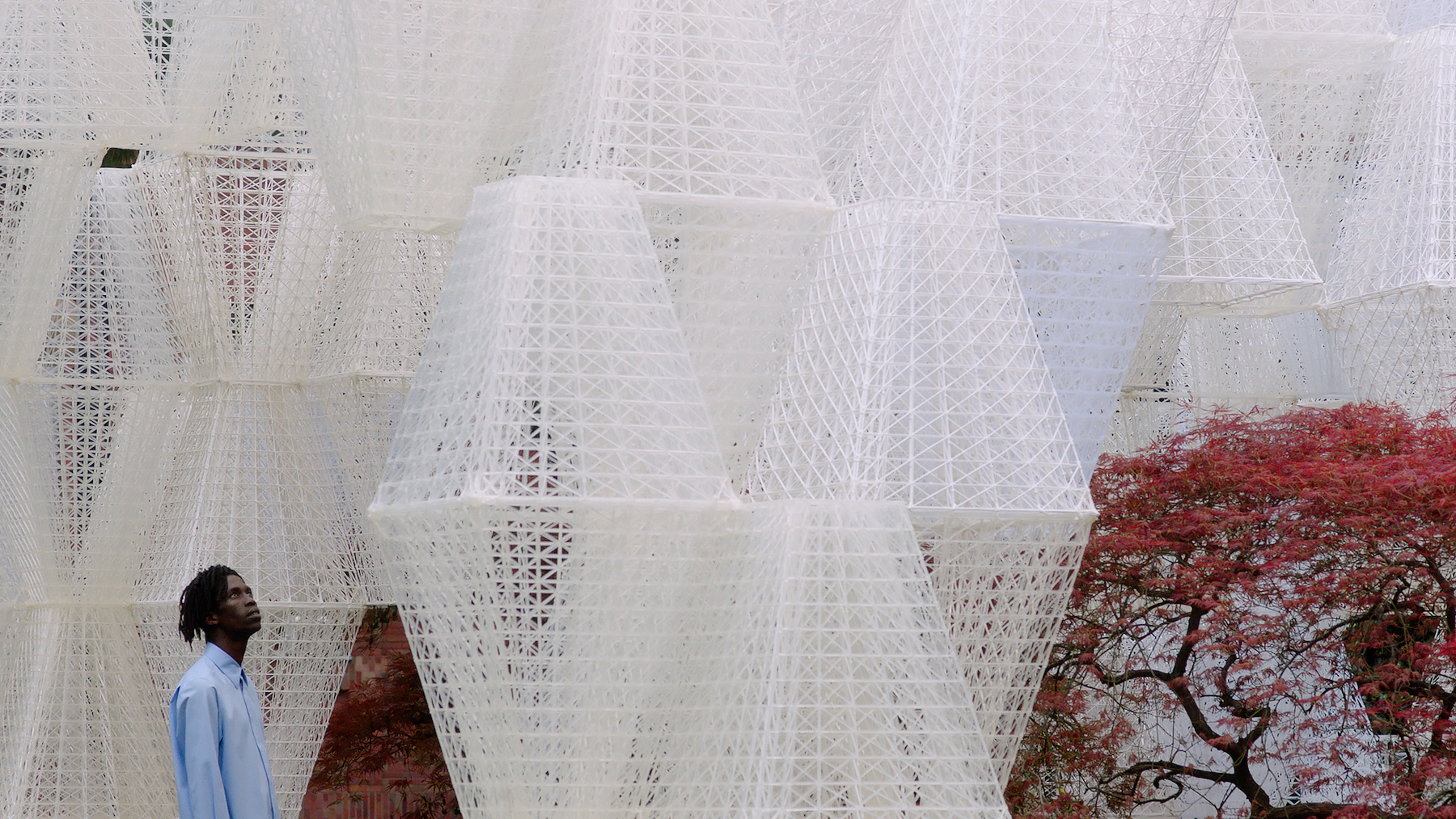
In terms of sustainability, what are designers getting right, and what can they improve?
KG: Our approach considers the implications of our products beyond the current season. We all need to take more responsibility in our day-to-day and realize the bigger picture.
AMM: Designers have a huge responsibility to take action and change the materials we use—for example, we need to minimize our use of concrete and steel, which have both become so abundant. The industry has been making some careless material decisions.
What do you hope attendees take away from experiencing Conifera?
KG: I hope they’ll enjoy the union—and perhaps tension—of the historic Palazzo Isimbardi versus something forward-thinking like Conifera, which has a real-world impact. Most of all, though, I hope everyone who experiences the pavilion will become curious about the possibilities of healthier, more sustainable production techniques.
AMM: I hope people will appreciate Conifera’s softness and lightness, and they feel at peace. I want to reassure everyone that imperfections are fine, and that an organic process can inform something quite magical. We brought a printer so people can understand this process better. I’m a teacher, so I designed Conifera to tell a story beyond just being itself.